This is the report of earlier "half system hot test". Probably 2020 or 2019. The difference of latest test from the earlier tests are the full load, the last step to a full engine test.
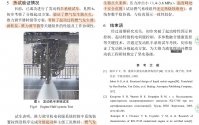
What are done in these tests:
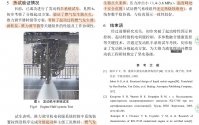
What are done in these tests:
- The gas generator is ignited.
- The ignition procedure is tested.
- Gas generator runs at a steady load.
- Turbopump and thrust adjustment device are tested.
- Temperature and thermal ablation of hot part are checked.