2020-07-28 22:32:03
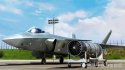
WS-15 codename Emei.
Speaking of the development of aero engines, the biggest gap between China and the United States was in the research and development model.
The development of aero engines in China is based on aircraft first and then engines. Engine development usually starts after the aircraft model is determined; while in the United States, engines are first developed after aircraft. When developing aircraft, there are already options available. engine.
It can be said that the development model of the United States is in line with the law of aeroengine development. This is because the technical difficulty of aeroengine development is much higher than that of aircraft, and the development time period is much longer than that of aircraft.
Two different R&D models have completely different consequences. Our country often falls into desperation because of the dismantling of aircraft models, and the engine eventually fails. In contrast, the American model is much better. Even if one or two aircraft models are dismantled, the development of engines cannot be stopped. Over time, it will naturally become a powerful engine country. .
Fortunately, the relevant departments of our country have recognized this importance. From the original research and development of aero engines as an important accessory part of aircraft, the importance of aero engines is on par with aircraft, and even It's even higher. To this end, the aero engine department has been independent from the aviation department, and a major special project "Aero Engine and Gas Turbine" has been set up to allocate a huge amount of money for research. Therefore, we have reason to be more optimistic about the future development of my country's aviation engines.
As you all know, WS-15, also called "Emei", is the standard engine of China's stealth fighter J-20. The first public report by official media was in 2017, on the evening of May 25th. The broadcast of CCTV "House of Craftsman" revealed that China's J-20 has been equipped with domestically-made engines, and at the end of the program, it said that from the third-generation mature engine "Taihang" series, it has developed by leaps and bounds to the fifth-generation "Emei" series. "The engine has amazed the world.
CCTV even used the words "wow the world amazed", which shows that the performance of WS-15 is indeed extraordinary.
In fact, the fifth-generation "Emei" engine mentioned in this CCTV report should be the fourth generation, that is, the F119 and F135 engines developed by Pratt & Whitney, both belong to the fourth generation; and the United States before F110, Russian AL-31, and China WS-10 belong to the third generation.
Regarding the performance of my country's WS-15 and American F119 and F135 engines, military expert Song Xinzhi once drew a table.
From the data in the above table, the afterburner thrust and thrust-to-weight ratio of WS-15 are already at the same level as the mass production model of F119 and the prototype of F135, but it is the same as the improved model of F119 and mass production of F135. There is still a gap.
The ratio of military thrust to afterburner thrust of F119 is about 0.67, the corresponding ratio of F135 is between 0.6-0.64, and the ratio of WS-15 is between 0.57-0.64. It seems to be equipped with WS-15 J- 20 fighters, super patrol capabilities may not be better than F-22 and F-35. In fact, because the J-20 is slender and adopts a duck layout, the aerodynamic characteristics of the transonic resistance are smaller, and the supersonic cruise lift-to-drag ratio is higher. According to the J-20 pilot's feedback, the supersonic flight characteristics of the fighter plane are very good, largely due to the excellent aerodynamic design of the J-20.
Looking at the bypass ratios of the three aviation engines again, the bypass ratio of F135 is more than double that of F119 and WS-15. This reflects that the F135's outer duct has a larger flow rate and a larger aircraft diameter. The advantage is that it is more fuel-efficient. The disadvantage is that the resistance is greater and the high-altitude thrust drops more. It is not good for achieving supersonic cruise and high maneuverability. From this point of view, F-35 is more suitable for use as an attack aircraft, and is not suitable for air control fighters.
Finally, let's look at the temperature before the turbine. The temperature before the turbine is the first process of the aero engine. An important indicator of the degree of temperature, under the premise of the same design level of the aero-engine turbine and fan, every time the temperature in front of the turbine increases by 100°K, the thrust increases by 15%. It can be seen that the temperature before the turbine has a great relationship with the engine thrust.
The temperature in front of the turbine of F119 aeroengine reached 1977K. It is estimated that the temperature in front of the turbine of F135 aeroengine is at the same level. The temperature before the turbine of the WS-15 is about 1850-1925K, which is close to the level of the two fourth-generation aircraft in the United States, but it is about 50-100K lower. This shows that the fourth-generation American aviation engine has higher thermal efficiency, better heat-resistant materials, and more advanced heat dissipation treatment for thermal components. Although the temperature in front of the turbine of WS-15 has been greatly improved, it still has a gap with the most advanced level, which shows that we will continue to work hard in heat-resistant materials and heat dissipation technology.
However, the F119 also achieved a maximum thrust of 17.4 tons in three stages. At the beginning, its test thrust was only 14.5 tons; in the second stage, it was relaxed to 15.6 tons; and finally it reached 17.4 tons. That is, continuously increase the maximum temperature before the turbine to achieve the purpose of increasing the push. However, due to the later development time of WS15, more mature powder turbine disk and single crystal blade technology are used. Especially the 65,000-ton mold section equipment ranks first in the world. Therefore, its turbine discs and blades can withstand higher temperatures for a long time. The first batch of afterburners with a small amount of off-line has reached 16.2 tons of thrust, exceeding the level of the second batch of F119 engines. Now the fourth batch may be off-line and installed for test flight, and it has been in line with the F119 increased version with about 18 tons of thrust. After the J-20 is installed in batches, it is bound to reach its peak!
That is to say, the performance of the subsequent batches of WS15 has begun to match that of the F119 in the United States. Besides, with the rapid development of new technologies today, it is entirely possible for us to overtake on corners in the future. So, finally, a new technology in our country, plasma flow control, is listed as one of the 10 cutting-edge aviation technologies by the American Academy of Aeronautics and Astronautics.
According to Li Yinghong, an academician of the Chinese Academy of Sciences, my country has made great progress in the field of plasma flow control. For aero engines, plasma flow control can prevent the most deadly surge in order to prevent the engine from stopping in the air. In fact, plasma flow control has long been developed and applied by some aviation powers, but the main problem is that it can only work at low speeds, not high-speed flow fields. Because it produces too little disturbance to the flow field, it is effective at low speeds. At high speeds, due to the relatively large momentum, the excitation disturbance is submerged and cannot interfere with the flow field.
For this reason, my country has established a special project to solve how plasma flow control works in high-speed flow fields. Finally, a discharge method that produces effective excitation in a high-speed flow field is developed. The basic principle is pulse discharge, which produces strong disturbances in a short period of time, and locally produces strong shock waves, that is, shock wave excitation, but because it is pulsed, the average power consumption is not very large, so the plasma flow is controlled from a low speed. Achieved high speed. Controlling the flow field through flow control can not only expand the stability margin of the engine, but also improve the aerodynamic performance of the aircraft.
Of course, so far, the plasma flow control of aircraft and engines is still in the laboratory stage, which is still far from actual use. However, we have reason to believe that my country will definitely make greater breakthroughs in this field.
Compared with traditional aero engine technology, in the field of plasma flow control, my country and the world's aviation powers started almost at the same time, there is no gap, and we have the advantage of leading the way. My country's future aero engine is worth looking forward to!